دسته بندی | کارآموزی |
بازدید ها | ۰ |
فرمت فایل | doc |
حجم فایل | ۱۴۳۸۳ کیلو بایت |
تعداد صفحات فایل | ۱۷۸ |
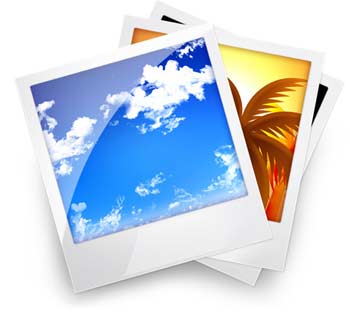
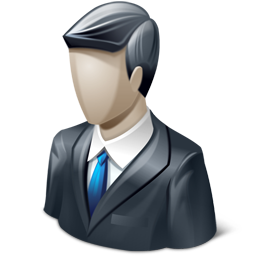
گزارش کارآموزی تولید کنسرو و رب گوجه فرنگی-گزارش از شرکت صنایع غذایی گلستان عصاره در ۱۷۸ صفحه ورد قابل ویرایش
فهرست مطالب
عنوان صفحه
چکیده ۱
بخش اول: کنسرو رب گوجه فرنگی ۲
مقدمه ۳
تاریخچه صنعت کنسرو ۴
تاریخچه کنسرو سازی در ایران ۵
تولید رب گوجه فرنگی ۶
فصل اول ۷
۱-۱ پیدایش گوجه فرنگی ۸
۲-۱ ترکیب شیمیایی گوجه فرنگی ۸
۳-۱ کشت گوجه فرنگی ۱۲
۴-۱ برداشت گوجه فرنگی ۱۳
۵-۱ حمل گوجه فرنگی ۱۴
فصل دوم: ۱۵
۱-۲ گزارش از شرکت صنایع غذایی گلستان عصاره تولید کننده رب گوجه فرنگی دلند ۱۶
۲-۲ نفشه ساختمانی شرکت ۱۸
۳-۲ روند تولید کنسرو رب گوجه فرنگی ۲۱
۱-۳-۲ دریافت گوجه فرنگی ۲۱
۲-۳-۲ شستشو ۲۱
۳-۳-۲ سورت کردن ۲۲
۴-۳-۲ خرد و له کردن ۲۳
۵- ۳-۲ حرارت مقدماتی ۲۳
۶-۳-۲ استخراج و تصفیه پالپ ۲۳
۷-۳-۲ تغلیظ آب گوجه فرنگی ۲۴
فهرست مطالب
عنوان صفحه
۴-۲ بسته بندی ۲۸
۱-۴-۲ بسته بندی قوطی ۲۸
۱-۱-۴-۲ افزودن نمک ۲۸
۲-۱-۴-۲ پاستوریزاسیون ۲۹
۳-۱-۴-۲ پر کردن ۲۹
۴-۱-۴-۲ دربندی قوطی ۳۰
۵-۱-۴-۲ تونل پخت ۳۱
۶-۱-۴-۲ تاریخ زدن ۳۱
۷-۱-۴-۲ بسته بندی قوطی ۳۲
۲-۴-۲ بسته بندی اسپتیک ۳۲
۵-۲ انبار ۳۳
فصل سوم: تأسیسات ۳۴
۱-۳ دیگ بخار ۳۵
۲-۳ کمپرسور هواسان ۳۷
۳-۳ سیستم آبرسانی ۳۸
۴-۳ سیستم فاضلاب ۳۸
۶-۳ سیستم اطفای حریق ۳۹
فصل چهارم: آزمایشات کنترل کیفیت ۴۰
مقدمه ۴۱
۱-۴ آزمایشات فیزیکوشیمیایی ۴۲
۲-۴ آزمون های میکروبی ۴۷
۳-۴ بررسی ویژگیهای ارگانولپتیکی ۴۹
۴-۴ ارزیابی دربندی قوطی ۴۹
۵-۴ آزمونهای آب ۵۲
۶-۴ فرم ارزیابی محصول ۵۵
فهرست مطالب
عنوان صفحه
بخش دوم: شیر و فراورده های آن ۵۷
فصل پنجم ۵۸
مقدمه ۵۹
۱-۵ تعریف شیر ۵۹
۲-۵ خواص فیزیکی شیر سالم ۶۱
۳-۵ اجزای اصلی شیر ۶۴
۴-۵ بی ثباتی ترکیبات شیر ۷۸
فصل ششم: گزارش از کارخانه پگاه گلستان تولید کننده شیر پاستوریزه و فراورده های آن ۷۹
۱-۶ معرفی کارخانه ۸۰
۲-۶ نحوه تأمین شیر مورد نیاز مجتمع ۸۴
۳-۶ جمع آوری و حمل شیر به کارخانه ۸۴
۴-۶ فرایند دریافت شیر خام ۸۵
۵-۶ اهمیت کیفیت بهداشتی شیر خام ۸۶
فصل هفتم: فرایند صنعتی شیر ۸۷
۱-۷ جداسازی چربی و تمیز کردن شیر ۸۸
۲-۷ هموژنیزاسیون ۸۸
۳-۷ عملیات حرارتی ۸۹
فصل هشتم: فراورده های تولیدی کارخانه ۹۲
۱-۸ شیر ۹۳
۱-۱-۸ شیر پاستوریزه ۹۳
۲-۱-۸ شیر استریلیزه ۹۴
۲-۸ ماست ۹۷
۱-۲-۸ خصوصیات شیر مصرفی در تولید ماست ۹۷
۲-۲-۸ استارتر در تولید ماست ۹۸
فهرست مطالب
عنوان صفحه
۳-۲-۸ مراحل تولید ماست ۹۸
۴-۲-۸ ساختار تشکیل ماست ۱۰۱
۳-۸ پودر شیرخشک و پودر آب پنیر ۱۰۴
۱-۳-۸ پودر شیرخشک ۱۰۴
۲-۳-۸ پودر آب پنیر ۱۰۷
۳-۳-۸ بسته بندی ۱۰۸
۴-۳-۸ موارد مصرف ۱۰۸
۵-۳-۸ کنترل کیفی ۱۰۸
فصل نهم ۱۰۹
۱-۹ نحوه نگهداری شیر و فراورده های آن ۱۱۰
۲-۹ مقایسه ارزش غذایی شیر خام، شیر پاستوریزه و شیر استریلیزه ۱۱۱
۳-۹ افزودنی های مجاز ۱۱۲
۴-۹ بازدارنده های رشد میکروبی ۱۱۲
فصل دهم: آزمایشات کنترل کیفیت ۱۱۴
۱-۱۰ آزمون های شیمیایی ۱۱۵
۱-۱-۱۰ اندازه گیری درصد چربی ۱۱۵
۲-۱-۱۰ اندازه گیری درصد پروتئین ۱۱۶
۳-۱-۱۰ تعیین ماده خشک ۱۱۷
۴-۱-۱۰ آزمونهایی که در هنگام دریافت شیر خام انجام می گیرد ۱۱۸
۵-۱-۱۰ تشخیص آنتی بیوتیک در شیر ۱۲۴
۶-۱-۱۰ تست فسفاتاز ۱۲۵
۷-۱-۱۰ تست پراکسیداز ۱۲۶
۸-۱-۱۰ تست آب اکسیژنه ۱۲۶
۹-۱-۱۰ تعیین درصد نمک ۱۲۷
فهرست مطالب
عنوان صفحه
۱۰-۱-۱۰ تعیین اسیدیته ۱۲۸
۱۱-۱-۱۰ تعیین غلظت سود و اسید ۱۲۹
۲-۱۰ آزمونهای میکروبی ۱۳۰
۱-۲-۱۰ آزمایش احیاء متیلن بلو در شیر خام (ردوکتاز) ۱۳۰
۲-۲-۱۰ آزمون اسپورکانت ۱۳۱
۳-۲-۱۰ شمارش کلی میکروبها (توتا) ۱۳۴
۴-۲-۱۰ روش شمارش و تشخیص کلیفرمها ۱۳۴
۵-۲-۱۰ روش جستجو و شناسایی اشریشیاکلی ۱۳۵
۶-۲-۱۰ شناسایی استافیلوکوکوس اورئوس ۱۳۶
۷-۲-۱۰ روش شناسایی کپک ها (کپک و مخمر) ۱۳۷
۸-۲-۱۰ تست فینگر ۱۳۸
۹-۲-۱۰ کشت آب مسیرهای CIP 138
۳-۱۰ فرم ارزیابی محصولات ۱۳۹
نتیجه گیری ۱۴۲
منابع و مآخذ ۱۴۳
ضمیمه ۱۴۴
بخش اول:
مقدمه:
غذا به عنوان یکی از نیازهای اصلی بشر و ارتباط مستقیم آن با سلامت و بقای او همواره مورد توجه بوده است.
انسان اولیه برای دستیابی به غذا مجبور بود به شکار بپردازد و یا از میوه ها و گیاهانی استفاده نماید که هیچ گونه شناختی نسبت به فواید و مضرات آنها نداشت، حتی گاهی مسافتها طولانی را می پیمود تا غذای خود را تأمین نماید. در نتیجه برای دسترسی آسان به غذا، به دامداری و کشاورزی روی آورد. اما این کافی نبود، رشد روزافزون جمعیت از یک سو و از سوی دیگر کمبود آذوقه در فصول دیگر و یا مواقع قحطی، نیاز تغذیه ای را بیشتر نمود.
این در حالی بود که وی در فصل برداشت و یا هنگام استفاده از گوشت حیوانات مقدار زیادی ازآن ها را به دلیل فاسد شدن دور می ریخته و یا به مصرف حیوانات اختصاص می داده است. پس باید چاره ای می اندیشید تا بتواند مازاد بر مصرف خود را به گونه ای به مدت طولانی تر حفظ نماید.
بنابراین چه باید می کرد؟ چگونه مشکل کمبود تغذیه را رفع نماید؟
چند راه ممکن بود:
۱- افزایش تولید ۲- جلوگیری از فساد ماده غذایی
۳- انبار کردن به مدت طولانی ۴- تنوع و گسترش منابع تغذیه ای
استفاده از این روشها می توانست راهکار مناسبی باشد.
از ابتدایی ترین روشهایی که برای جلوگیری از فساد برگزید خشک کردن در زیر نور آفتاب و به مرور زمان دودی کردن، نمک سود کردن و … بوده است.
از طرفی انتخاب واریته هایی با میزان تولید بیشتر و پرورش آنها کمک شایانی به افزایش تولید نمود.
استفاده از انبارهای سرد و تاریک (با نور کم) نیز تا حدی برای افزایش مدت ماندگاری محصول مناسب می نمود اما باز هم قسمت اعظم محصولات فاسد و غیرقابل استفاده می شد.
گسترش و تنوع در غذا به عنوان مثال پی بردن به فرایند تخمیر و تولید ماست، پنیر و نان از دیگر عوامل مؤثر بوده است.
تمامی این روشها تغییرات زیادی یافتند و نتایج مفید آنها بشر را در پیشبرد اهداف عالی و کاستن نقصها سهیم ساخت.
بعدها به ارتباط بعضی بیماریها و مصرف غذاهای آلوده پی برد و با تحقیق، مطالعات و آزمایشات فراوان به وجود میکروارگانیسمها و تأثیر آنها در فساد مواد غذایی آگاهی یافت و برای از بین بردن آنها دریافت اعمال حرارت، ایجاد خلاء و رعایت اصول بهداشتی و … می تواند مؤثر واقع شود.
به این ترتیب با تکامل بشر و پیشرفت او درعلم، به تدریج روشها، ابداعات و اختراعات ارزنده ای برای بهبود کیفیت، جلوگیری از فساد و افزایش مدت ماندگاری مواد غذایی صورت گرفت و بالاخره صنعت غذا هم در کنار دیگر صنایع پا گرفت و روبه پیشرفت نهاد.
چنانکه امروزه شاهدیم، با تکنولوژی پیشرفته؛ خشک کردن، انجماد سریع پاستوریزاسیون، استریلیزاسیون، کنسرواسیون، بسته بندی اسپتیک، سیستمهای فراپالایش و … در شرایطی کاملاً بهداشتی، در مدت زمانی اندک و میزان زیاد تولید انجام می گیرد.
وجود انبارهای مکانیزه و سردخانه های زیر صفر نگهداری محصولات را به مدت طولانی بدون آنکه آسیب چندانی به بافت آنها برساند امکان پذیر ساخت.
همچنین علم ژنتیک با بررسی نژادها، گونه ها و واریته های مختلف به اصلاح نژاد پرداخت و موالیدی با بازدهی بالا ایجاد نمود.
بنابراین همگام با صنایع غذایی دیگر علوم مرتبط با آن نیز یاری نموده و صنعت غذا را تا جایی پیش برد که بشر امروز بتواند به غذایی سالم با تنوع زیاد با حفظ حداکثر ارزش غذایی، دسترسی آسان داشته باشد.
در این گزارش به صنعت تولید کنسرو رب گوجه فرنگی پرداخته شده است امیدوارم با توجه به مدت زمان کوتاه در گردآوری مطالب تا حدی مفید، موفق بوده باشم.
– تاریخچه صنعت کنسرو
کلمه کنسرو از لغت یونانی «conservar» به معنی محافظت کردن گرفته شده است. بنابراین می توان گفت که هدف از کلمه کنسرو کردن در صنایع غذایی ایجاد شرایطی است که بتوان تحت آن شرایط محصول مورد نظر را برای مدت طولانی نگهداری نمود.
تاریخچه کنسرو سازی به سال ۱۷۹۰ که دولت فرانسه با کشورهای اروپایی در حال جنگ بود برمی گردد(۲).
بیماری اسکوربوت، افراد نیروی دریایی فرانسه را رنج می داد. این اوضاع نابسامان دولت فرانسه را واداشت تا جایزه ای معادل ۱۲۰۰۰ فرانک برای کسی که روش نگهداری مواد غذایی را بیابد، تعیین کند(۳).
تا این که در سال ۱۷۹۸ قناد فرانسوی به نام نیکلاس اپرت که امروزه بنام پدر کنسروسازی معروف است با ابداع روش مناسبی، مشکل را حل کرد. وی دریافت که اگر مواد غذایی را در داخل قوطی سربسته حرارت بدهند و پس از آن هوا به داخل ظرف نفوذ نکند زمان ماندگاری غذا به نحو چشمگیری افزایش می یابد.
آپرت در سال ۱۸۱۰ نتیجه تحقیقات خود را در کتابی به نام «L,Art de coserve» منتشر کرد که کلیات آن در ۴ ماده ذیل خلاصه شده بود:
۱- تمیز کردن و گذاشتن مواد غذایی که قصد کنسرو کردن آنها را داریم در داخل ظروف شیشه ای
۲- درب بندی دقیق این ظروف به وسیله چوب پنبه
۳- قرار دادن این ظروف در داخل آب جوش به مدت های مختلف، بسته به نوع ماده غذایی
۴- بیرون آوردن ظروف و سرد کردن آنها. (۲)
وی از جزئیات عمل خود در جلوگیری از فساد به درستی آگاه نبود. به مرور، مقالات متعددی در این مورد نوشت و در یکی از آنها به نقش دما در از بین بردن و عقیم کردن آنزیمها اشاره نمود.
اما پاستور دانشمند بزرگ فرانسوی با مطالعات فراوان ثابت کرد که نقش اصلی این عمل در جلوگیری از فساد، اثر دما بر روی میکروارگانیسمها است(۱).
مطالعات بر روی کنسرو کردن مواد غذایی در نتیجه عمل اپرت رو به فزونی نهاد و به نتایج چشمگیری دست یافت.
ظروف لعابی به جای ظروف شیشه ای متداول گردید. فوستییر روش لحیم کردن قوطیهای فلزی را اختراع نمود و در سال ۱۸۵۱ آبردین با اضافه کردن مقداری محصول غلیظ نمک و املاح دیگر توانست دمای استریلیزاسیون را به بیش از ۱۰۰ درجه بالا ببرد.
تا اینکه در سال ۱۸۷۴ دیگ بخار توسط پاپن و اتوکلاو توسط شریور اختراع گردید (۱).
و امروز در جهان نگهداری مواد غذایی پیشرفت زیادی کرده است و روشهای بیشماری مورد استفاده قرار می گیرد تا جایی که امروزه از فروشگاه های مواد غذایی می توان انواع مواد غذایی مربوط به سراسر دنیا را بصورت آماده و یا نیمه آماده خریداری و در ظرف مدتی کمتر از ۱۰ دقیقه به کمک تکنولوژی جدید پخت و پز، انواع غذاهای خوش رنگ و خوش طعم و خوشمزه را تهیه نمود و این امر را بایستی مدیون تکنولوژیستهای صنایع غذایی باشیم (۴).
– تاریخچه کنسروسازی در ایران
تا قبل از سال ۱۳۱۰ در ایران کسی با این صنعت آشنایی نداشته است تا اینکه در سال ۱۳۱۶ اولین کارخانه کنسروسازی برای تولید کنسرو ماهی در بندرعباس تأسیس شد. در سال ۱۳۱۹ یک کارخانه کنسرو گوشت و سبزیجات در شمال ایران، در قائمشهر احداث شد و محصولات آنها بیشتر برای نیروهای ارتش مصرف می شده است.
از سال ۱۳۴۰ تا سال ۱۳۴۸ رشد صنایع کنسروسازی چشمگیرتر بوده و سیر صعودی داشته است. در این سالها شرکت آتاکو با وارد کردن خط تولید رب گوجه فرنگی تحولی در تولید محصول مزبور بوجود آورد. (۴)
در حال حاضر تعداد کارخانه های کنسروسازی کشور متجاوز از ۱۵۰ واحد می باشد.
به طوری که تنها کارخانجات تولید رب گوجه فرنگی در نقاط مختلف کشور سالیانه با ظرفیتی بالغ بر ۲۰۰۰۰۰ تن فعالیت دارند (۴).
– تولید رب گوجه فرنگی:
توسعه و گسترش واقعی رب گوجه فرنگی بعد از جنگ جهانی دوم در سال ۱۹۴۷ صورت گرفت.
در سالهای اخیر تقاضای جهانی برای مصرف گوجه فرنگی رو به افزایش بوده است و از کل مقدار تولید شده ۶۰ درصد صنایع تبدیلی مصرف شده است.
در بین فراورده های گوجه، رب گوجه فرنگی کاربردش بیشتر است و به نام توصیفی ژنریک آب گوجه فرنگی غلیظ شده با مواد جامد محلول ۲۸ تا ۳۰ درصد (Double, tomato paste) و ۳۶ تا ۴۰ (triple tomato paste) به فروش می رسد (۳).
الف- کربوهیدرات ها
میزان پلی ساکاریدهای گوجه فرنگی حدود ۷/۰ درصد می باشد که ۵۰% آن را پکتین و آرابینوگالگتن تشکیل می دهد و حدود ۲۵% گزیلن و آرابینوگزیلن و ۲۵% باقی مانده را سلولز تشکیل می دهد.
حدود ۵۰ تا ۶۰ درصد مواد جامد محلول گوجه فرنگی را قندهای احیاء کننده (گلوکز و فروکتوز) تشکیل می دهد.
ب- پروتئین و اسید آمینه
حدود ۱۱ اسید آمینه در گوجه فرنگی مشخص شده است که فقط ۴۵ درصد این اسیدهای آمینه را اسید گلوتامیک تشکیل می دهد.
دومین اسید از نظر مقدار اسیدآسپارتیک می باشد. در تهیه محصولات گوجه فرنگی وقتی که آب گوجه فرنگی به مدت ۲۰ دقیقه در حرارت ۱۰۰ درجه سانتی گراد می ماند، باعث هیدرولیز پروتئین ها و آزادشدن اسیدهای آمینه می شود. مثلاً گلوتامین یک NH3 از دست می دهد و به اسید گلوتامیک تبدیل می شود و عاملی که باعث افزایش آمونیاک در آبگوجه فرنگی بسته بندی شده در قوطی می شود همین مورد است گلوتامین و آسپارژین می توانند در اثر از دست دادن آمین و تغییر فرمول به اسید پیروکیدون تبدیل شوند.
ج- اسید
اسید گوجه فرنگی عمدتاً اسیدسیتریک است، روی این اصل اسیدیته آن برحسب اسید سیتریک محاسبه می شود. اسیدهای دیگری هم مثل اسیدمالیک و اسیدتارتاریک در گوجه فرنگی وجود دارند. ضمن عمل تولید و تهیه آب گوجه فرنگی اسیدیته، کل افزایش پیدا می کند، مثلا: اسیداستیک به میزان ۳۲ درصد افزایش پیدا می کند. این افزایش در اکسیداسیون آلوئیدها و الکلها می باشد.
د- ویتامین ها
۱- ویتامین C: میزان ویتامین ث گوجه فرنگی بین ۱۰ تا ۶۰ میلی گرم در ۱۰۰ گرم گوجه فرنگی است. گوجه فرنگی های رسیده در مقابل نور خورشید حداقل دارای ۳۰ میلی گرم ویتامین ث می باشد.
۲- میزان ویتامین K بین ۱/۰ تا ۶/۰ میلی گرم در یک کیلوگرم گوجه فرنگی می باشد.
۳- ویتامین A: مواد رنگی گیاهان
مواد رنگی گیاهان به دو دسته قابل حل در چربی و قابل حل در آب تقسیم می شوند. رنگ گوجه فرنگی جزو دسته اول (قابل حل در چربی) می باشد و آنها را کاروتنوئیدها می نامند؛ و ریشه آن کاروتن یا پلی ویتامین A می باشد.
کاروتنوئیدهای قرمز شامل لیکوپن و کاروتنهای آلفا و بتا می باشد که فرمول کلی آنها C4oH56 است و کاروتنوئیدهای نارنجی دارای فرمو ۰C4oH56 می باشند و از نظر شیمیایی اختلاف چندانی بین دو نوع کاروتنوئید وجود ندارد.
گوجه فرنگی هایی که رسیدن آنها در درجه حرارت بین ۲۰ تا ۳۰ درجه سانتی گراد صورت می گیرد حدود ۱۰ مرتبه بیشتر از حد معمول کاروتن بتا را دار می باشند و چنانچه رسیدن گوجه فرنگی در حرارت ۳۵ درجه سانتی گراد صورت پذیرد مقدار کاروتن آن مساوی لیکوپن می شود.
رنگ لیکوپن قرمز درخشان است درصورتی که کاروتن بتا دارای رنگ قرمز نارنجی است . بتاکاروتن بهترین نوع ویتامین A می باشد و یک مولکول آن پس از هیدرولیز تبدیل به دو مولکول ویتامین A می شود . انسان به آسانی می تواند بتاکاروتن را تبدیل به ویتامین A نماید . هرچه گوجه فرنگی ریزتر باشد مقدار بتا کاروتن آن بیشتر است .
۶ – ۷ – ۳ – ۲ – شستشوی مخازن:
برای شستشوی مخازن ابتدا آب داخل آنها ریخته شده، سپس از بالا به آن بخار تزریق می گردد تا به دمای ۸۰ درجه سانتی گراد برسد . به مدت ۲۰ دقیقه سیرکوله شده سپس آب تخلیه می گردد.
در پایان اگر شستشو کافی نبود از سود ۳% استفاده نموده و به مدت ۴۰ دقیقه همراه با آب و بخار شستشو صورت می گیرد. بعد از تخلیه مجدداً با آب داغ شستشو داده تا باقیمانده سود شسته شود. سپس pH آنرا اندازه گیری نموده اگر باز هم اثر قلیا در آن وجود داشت با آب و بخار شسته شده و از اسید برای خنثی نمودن اثر قلیا استفاده می گردد و مجدداً شستشوی نهایی صورت می گیرد.
۴ – ۲ – بسته بندی :
در این کارخانه دو نوع بسته بندی وجود دارد:
۱) بسته بندی قوطی ۲) بسته بندی اسپتیک
۱- ۴ – ۲ – بسته بندی قوطی
برای بسته بندی رب در قوطی بریکس رب در اواپراتورها به ۲۶ – ۲۵ می رسد و قبل از بسته بندی ابتدا به آن نمک افزوده می شود.
۱ -۱ – ۴ – ۲ – افزودن نمک:
رب گوجه با بریکس ۲۵ وارد مخازن فرموله شده و در آنجا به میزان ۳ – ۲ درصد نمک به آن افزوده می شود.
این مخازن استوانه ای شکل بوده که در پایین مخروطی می شود در هنگام تولید تا قسمت مخروط همیشه رب وجود دارد و هنگام تخلیه رب به مخزن پاستوریزه، هیچگاه قسمت مخروط خالی نمی شود.
این مخزن توسط پمپهای سانتریفوژی که نیروی گریز از مرکز دارند، عمل می نماید و اگر قسمت مخروطی خالی شود هوا به این قسمت وارد شده و فشار هوا کم می شود آنگاه پمپها فعالیت نمی کنند. بنابراین با پر بودن قسمت مخروطی مخزن فشار لازم جهت فعالیت پمپها تأمین می شود.
این مخزن حدود ۸۰۰/۱ تن گنجایش دارد. قسمت مخروط آن تا ۳۰۰ تن گنجایش داشته و معمولاً در اول تولید که قسمت مخروطی شکل پر می شود ۱۴ کیلوگرم به آن نمک زده می شود. از قسمت مخروط به بعد بر روی بدنه مخزن نشانه گذاری شده است، اعداد به ترتیب از ۵ تا ۴۵ (… و ۱۵ و ۱۰ و ۵) شماره گذاری می شود. به این منظور هرگاه رب به هر کدام از این خطوط می رسد ۵ کیلوگرم نمک افزوده می شود. وقتی مخزن کاملاً پر شود به آن ۴۵ کیلوگرم نمک زده شده است.
افزودن نمک به رب باعث افزایش مدت ماندگاری محصول می شود نمک از جمله موادی است که فعالیت آب را کاهش داده و محیط را جهت فعالیت میکروارگانیسم ها نامناسب می سازد. از طرفی افزودن نمک عامل طعم دهنده به رب نیز می باشد.
بعد از افزودن نمک بریکس به ۲۸ – ۲۷ می رسد. از مخزن فرموله رب توسط پمپ به مخزن پاستوریزه منتقل می شود.
۲ – ۱ – ۴- ۲ – پاستوریزاسیون:
رب از مخزن پاستوریزه به طور مداوم به دستگاه پاستوریزاتور تزریق می شود.
پاستوریزاتور از نوع لوله ای بوده که بصورت رفت و برگشتی می باشد. در داخل این لوله ها، لوله باریکتری قرار دارد که رب داخل لوله باریک و بخار با دمای ۸۵ درجه سانتی گراد در پشت آن در جریان است در اثر تماس غیرمستقیم محصول با بخار داغ دمای محصول به ۸۲ درجه سانتی گراد رسیده و در نتیجه بسیاری از میکروارگانیسمها از بین می روند و رب سالم سازی می شود و مدت ماندگاری آن افزایش می یابد.
از طرف دیگر وقتی محصول با این دما دربندی می شود عمل خارج کردن هوا نیز انجام می گیرد در نتیجه این عمل اکسیژن موجود در محصول خارج شده و از فساد شیمیایی محصول جلوگیری به عمل می آید همچنین بعد از دربندی و خنک شدن قوطی به دلیل تقطیر شدن بخارات در فضای بالای قوطی خلاء نسبی ایجاد می گردد. همه این عوامل در افزایش کیفیت نهایی محصول و حفظ ارزش غذایی آن مؤثر خواهد بود (شکل ۱۳ – ۲).
۳ – ۱ – ۴ – ۲- پر کردن :
رب گوجه پس از پاستوریزاسیون به دستگاه فیلر منتقل می گردد. این دستگاه ۸ پیستون داشته و نیروی لازم برای عمل پیستونها از طریق فشار هوا تأمین می گردد. اگر فشار هوا کافی نباشد دستگاه متوقف می شود.
در این مرحله قوطی ها که در طول مسیر به علت تزریق بخار و هوا فاقد هر گونه آلودگی بوده توسط دستگاه فیلر به اندازه ظرفیت خودپر می شوند (شکل ۱۴ – ۲).
اپراتور دستگاه دما و وزن هر ۸ پیستون را بطور مداوم بررسی نموده و واحد کنترل کیفیت نیز هر ۳۰ دقیقه علاوه بر وزن و دما، درصد نمک و بریکس را هم کنترل می نماید.
معمولاً در مورد قوطیهای ۱۰۰۰ گرمی، وزن قوطی با درب آن ۹۸۰ – ۹۷۲ و دمای رب ۸۴ – ۸۲ می باشد. درصورت تنظیم نبودن دما، وزن قوطی ها ممکن است بالاتر و یا پایین تر از این مقدار باشد.
اگر دمای رب از این مقدار بالاتر باشد وزن قوطی پایین آمده و از طرفی در هنگام دربندی و سرد شدن آن فضای خالی سر قوطی زیاد شده و ممکن است در اثر خلاء در قوطی فرورفتگی ایجاد شود. همینطور اگر دما پایین باشد وزن قوطی بالا می رود.
در ماشینهای دربندی اتوماتیک تمامی عملیات از قبیل قرار گرفتن قوطی ها در دستگاه و یا گذاشتن درپوش آنها بصورت خودکار انجام می گیرد. به این ترتیب که قوطی های پر شده روی یک نوار نقاله که سرعت حرکت آن برحسب کار دستگاه دربندی تنظیم شده است حمل شده و از یک نقاله کوچک قلاب دار که قوطی ها را از هم جدا می کند، عبورمی کنند. در این نقاله قوطی ها در وضع متناسب با حفره های کفه ورودی دستگاه دربندی قرار می گیرند. سپس توزیع کننده خودکار درپوش، شامل یک کاردک با حرکت رفت و برگشتی و یک شستی، سرپوش ها را روی قوطی ها قرار داده و بعد توسط قرقره های اولیه و ثانویه که ضمن چرخیدن دور خود، دور سر قوطی هم می گردند عمل دربندی انجاممی گیرد(۲).
در این کارخانه این ماشین ها مجهز به چهار سر سیاره ای بوده که می تواند در ۲۴ ساعت ۱۰۰ – ۸۰ هزار قوطی را دربندی نماید.
اصول دربندی مضاعف
۱- مرحله اول:
در این مرحله قرقره های اولیه بین ۵ الی ۹ بار دور قوطی دوران می کنند و در نتیجه قلاب های سر و بدنه تشکیل شده و قلاب سر، قلاب بدنه را می پوشاند. در مرحله اول تقریباً ۷۵ درصد عملیات دوخت انجام گرفته است. در پایان این مرحله یک درز با مقطع گرد حاصل می گردد.
۲- مرحله دوم
در مرحله دوم، قرقره های ثانویه بین ۳ الی ۷ بار دور قوطی و بر روی محیط دوخت حاصل از مرحله اول دوران می کند. در اثر عملیات فوق، دوخت مقدماتی فشرده شده و پهن می گردد. به این ترتیب درز کامل جفت شده و به حالت غیرقابل نفوذ درمی آید.
برای انجام یک دربندی صحیح رعایت نکات زیر ضروری است:
۱- ضخامت حلب ورق قوطی و سر باید یکنواخت باشد.
۲- اندازه قلاب بدنه و قلاب سر تقریباً مساوی و در حد استاندارد باشند. سایر پارامترهای درز مانند: طول دوخت، ضخامت دوخت، عمق دوخت، درصد درگیری و میزان فضای آزاد نیز باید در اندازه استاندارد باشد. ماده لاستیکی درب قوطی نیز باید یکنواخت و دارای قشر کافی باشد.
۳- ماشین دربندی کاملاً سالم بوده و بخصوص دیسک و قرقره های آن فرسوده نشده باشد و ارتفاع پایه و فاصله قرقره ها از دیسک تنظیم شده باشد. تنظیم دستگاه دربندی برای انجام صحیح عملیات از اهمیت به سزایی برخوردار است. بنابراین به صورت روزانه تنظیم دستگاه صورت می گیرد (۲) .
از دو دستگاه دربندی که در حال حاضر از آنها استفاده می شود بصورت روزانه نمونه های قوطی خالی که دربندی شده اند آورده می شود و توسط واحد کنترل کیفیت عمل دربندی آن بررسی می گردد. در صورت عدم تطابق با حد استاندارد در هر قسمت مجدداً دستگاه تنظیم می شود که گاهی این عمل چندین بار تکرار شده تا زمانی که عمل دربندی صحیح انجام شود.
۵ –۱- ۴ – ۲ – تونل پخت (پاستوریزاسیون ثانویه)
پس از مرحله دربندی قوطی ها با حرکت بر روی نوار نقاله به سمت الواتورها می روند در این قسمت قوطیها بصورت افقی روی طبقات الواتور قرار گرفته و وارد تونل می شوند. (شکل ۱۷ – ۲). در داخل تونل به مدت ۲۰ دقیقه به صورت غلتان ابتدا از زیر آب جوش ۹۲ – ۹۱ درجه سانتی گراد و سپس آب ۸۰ درجه و در نهایت در طبقه زیرین تونل از زیر دوش های آب سرد عبور می کنند. دمای قوطی ها بعد از گذر از تونل به ۴۰ – ۳۵ درجه سانتی گراد می رسد. در این دما قطرات باقیمانده آب روی قوطی ها تبخیر شده و مشکل زنگ زدگی در آینده ایجاد نخواهد شد.
۶ – ۱- ۴ – ۲ – تاریخ زدن:
قوطی ها پس از خارج شدن از تونل پخت با حرکت روی نوار نقاله به سمت انبار بسته بندی هدایت می شوند. در طول این مسیر از زیرجت پرینتر عبور می کنند. این دستگاه توسط چشم الکترونیک عمل نموده و بر روی درب قوطی، تاریخ تولید و انقضاء، سری ساخت، ساعت تولید، قیمت محصول و مهر استاندارد را درج می نماید. تاریخ هم بصورت میلادی و هم فارسی زده می شود.
۷ – ۱ – ۴ – ۲ – بسته بندی قوطی ها:
پس از عبور از جت پرینتر قوطی ها به انبار بسته بندی وارد می شوند. در ابتدا کارگران تاریخ و ساعت تولید درج شده روی درب را کنترل نموده سپس بسته به نوع قوطی (۵۰۰ یا ۱۰۰۰ گرمی) آنها را در بسته های ۱۲ یا ۲۴ تایی قرار داده و برای تکمیل عمل بسته بندی، به شرینگ پک منتقل می شوند. این دستگاه تحت فشار هوا کار می کند به این صورت که نایلون روی بسته کشیده می شود و لبه های آن توسط فشار هوای ایجاد شده دوخته می شود. سپس این بسته ها از زیر محفظه ای عبور می کنند که در آن المنتهایی تعبیه شده است که حرارت بالا تولید نموده و باعث می شود نایلون به طور کامل بسته را بپوشاند. سپس توسط کارگران بسته ها روی پالت چیده شده و به انبار انتقال می یابند (شکل ۱۸ – ۲).
۲ – ۴ -۲ – بسته بندی اسپتیک:
نوع دیگر تولیدات کارخانه گلستان عصاره تولید و بسته بندی رب در کیسه های اسپتیک است. ماشین آلات این نوع بسته بندی از کشور ایتالیا و شرکت FBR می باشد.
اسپتیک از دو قسمت اصلی تشکیل شده است: یکی استریلایزر و دیگری فیلر.
در واقع این دستگاه قادر است تمام میوه ها را به صورت پوره یا کنسانتره استریل کرده و بسته بندی نماید.
برای بسته بندی اسپتیک، غلظت رب به وسیله اواپراتورهای سه مرحله ای بسیار پیشرفته به بریکس ۳۸ – ۳۶می رسد. در این مرحله حفظ غلظت رب در این بریکس بسیار مهم است. این عمل توسط سیستمهای کاملاً خودکار انجام می شود.
بدین منظور رب ابتدا وارد قسمت استریلایزر می شود که خود شامل بخشهای: هیتینگ ، هلدینگ و کولینگ می باشد.
رب گوجه با گذر از قسمت هیتینگ به درجه حرارت استریل یعنی ۱۰۸ درجه سانتی گراد می رسد. سپس در قسمت هلدینگ مدت زمان لازم را سپری نموده و در قسمت کولینگ به درجه حرارت مناسب برای پر شدن یعنی ۳۵ درجه سانتی گراد می رسد. بعد از آن رب گوجه به قسمت فیلر رفته و در آن جا در یک محیط کاملاً استریل به وسیله هدهای دستگاه فیلر در کیسه های اسپتیک در اوزان ۲۰۰ و ۲۰ لیتری پر می شود. این محصول به مدت ۲ سال قابل نگهداری است.(شکل ۱۶ – ۲)
۵ – ۲- انبار:
محصولات تولید شده و مواد اولیه در انبار نگهداری می شوند.